>>
ATLANTIC CROSSING
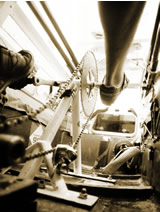 |
For
the Atlantic crossing we cobbled together a system that comprised
a conventional cog and chain arrangement married to a bevel
box transmitting power through 90 degrees to a steel propeller
shaft and ultimately a 17-inch, 2 x bladed aluminium propeller.
An A frame in the middle of the boat held a specially
designed bearing system impervious to the harsh effects of saltwater.
High-tech synthetic grease was used on all moving surfaces to
keep the whole thing working.
- Frame:
custom chrome moly A frame built by Sonic Cycles
in London.
- Chainring:
custom 60 deep tooth stainless steel one-piece cog.
- Crank:
Shimano Dura-ace 175mm.
- Bottom
bracket: Shimano Dura-ace fitted with custom grease flushing
system.
- Rear
cog: 12 tooth stainless steel.
- Grease:
Black and Gold synthetic Q40
|
WEAKNESSES
Although
we never had to resort to using the oars, serious flaws in the propulsion
design began to appear towards the end of the Atlantic voyage prompting
us to consider a revised system for the Pacific. These included:
1.
Significant friction losses from the many moving surfaces required
to transfer power from the cranks to the propeller blades. These
included the bottom bracket, 2 x chain to sprocket interfaces, 1:1
ratio worm gearing inside the bevel box, a deep-sea seal to exit
the steel prop-shaft from the hull and a marine seal holding the
same shaft inside the skeg.
2.
The prop-shaft was hopelessly exposed to potential damage from a
length of submerged timber or surfacing whale.
3.
Towards the end of the voyage a gasket seal on the side of the bevel
box failed causing the lubricant to leak out. This led to over heating
and subsequent expansion of the bearings making the pedaling at
times impossible. We then found to our dismay that the unit was
sealed and the only way of introducing replacement lubricant was
to run drips of cooking oil down a cotton thread into a narrow opening
where the gasket seal once was!
So the criteria for a new system would be
minimum friction loss and ease of servicing, replacement of new
parts or the whole system if need be. The main challenge proved
to be engineering a way to transfer the drive through 90 degrees
and from the pedal cranks above the water line to the propeller
below the water line. We had limited success experimenting with
twisted quarter inch chains, but finally found a solution in the
form of a direct-drive, all-in-one
unit.
>>
FIND OUT HOW THE PROPULSION SYSTEM WAS IMPROVED FOR THE PACIFIC
CROSSING >>
>>
back to THE
PEDAL BOAT
|